CORROSION EXPERTISE: ARE YOU SUFFICIENTLY INFORMED TO MAKE DECISIONS?
BY HERBERT H. DEFRIEZ, PE
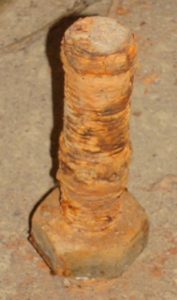
Corrosion, everybody knows what it looks like, just like the bolt shown on the right; it looks in really bad shape and if the corrosion was caused by a leak that your company insured against, this could be costly.
But what about things that don’t look like corrosion. Take the photo to the lower right for example. You find this piece lying on the ground after a plant accident. Looks like a mechanical failure of a brittle section of perhaps a torque tube – was this where the problem started? You take a good look, note the crystalline nature of the fractures, note the many fissures in the metal, note that the metal is mostly shiny and shows no signs of “rust”. If you concluded that this was a mechanical failure due to overstressing,
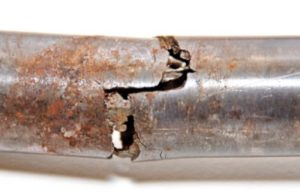
you would be completely wrong. This is a section of Type 316 Stainless Steel tubing carrying smoke stack gases to an analyzer. The fractures are actually chloride-induced stress corrosion cracking and the disruption was caused when a pipe fitting was being removed by hand. Not your culprit at all.
And these revelations about corrosion can go on and on. To give you the most basic insight into the potential problems in assessing corrosion, let’s start by just listing the nine general forms of corrosion, (probably many more than you thought and way more than you wanted to know). Corrosion comes in the following forms: 1) Uniform (like bolt shown); 2) Localized (pitting); 3) Galvanic (connecting brass to steel); 4) Velocity Induced; (erosion corrosion) 5) Intergranular; 6) De-Alloying; 7) Cracking; 8) High Temperature and 9) Microbial. The items not followed by an example are the more difficult types to evaluate and often require sophisticated analysis to determine. If your company has corrosion exclusions in its property policies, could you recognize if corrosion were involved and recommend a cause and origin investigation?
An actual example involves a sail boat mast failure in high winds. Clearly the cause was the wind but the policy had a corrosion exclusion. The broken section was sent for evaluation. Dismantling the stainless steel sail retainer and its stainless rivets from the aluminum mast exposed exterior corrosion at each rivet hole. Micro sectioning also reveled cracking around each hole; these cracks were the probable initiation point for a massive tension failure. Perhaps without the corrosion induced cracks, the mast would not have failed? The insurance company did not pay.
Fortunately, your I-ENG-A family of investigators has a Registered Corrosion Engineer – myself. I can work through your local investigator to provide evaluations of simple-to-complex corrosion problems. Once engaged, I would prepare inspection, photograph and interview criteria for the local investigative engineer to perform on-site. Over 80 percent of the time, the origin and cause can be determined over the Internet using this locally collected data. Should the problem exceed this approach, I can also travel to photograph and retrieve samples for sophisticated chemical and physical analysis. Should subrogation become an issue, I am also a court-tested expert witness. Contact your local I-ENG-A member for details.
By the way, about the bolt. You would most likely have been wrong about it as well. This bolt was submerged in water for nearly two years in a newly poured concrete footing sump. The water’s alkalinity prevented most of the uniform corrosion that would have occurred under other circumstances. After drying out, the bulk of the “corrosion” appeared to be silt and hydrated lime, easily removed with a wire brush. The cleaned bolts would easily accept new nuts. To verify that the bolts were still suitable for their originally intended purpose, in-place pull tests were performed; these tests indicated the bolt’s strength was still in excess of design specifications. After only cleaning, the bolts were returned to service. These results would have saved you a lot of money.
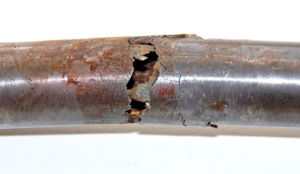
About the Author:
Mr. Herbert H. DeFriez, P.E., graduated from the University of California, Berkeley, with a BS in Chemical Engineering in 1966 after surviving the Free Speech Movement and Mario Savio standing on a police car in Sproul Plaza. Disliking chemical engineering, his first job was as a corrosion engineer with American Potash and Chemical in Trona, CA. Since there were no women above high school age in town (if you have been to Trona, you know why), he returned to chemical engineering as an experimental operations engineer with Shell Development in Albany, CA. With the Vietnam War at its height and Mr. DeFriez’s allergy to bullets, he joined the U.S.Public Health Service as alternate service where he learned industrial hygiene sampling – this lead to the beginning of his career in environmental engineering. First as an employee that developed an air and water testing laboratory, then as a consultant to that laboratory, then on to developing a design and manufacturing company that built air sampling and testing equipment and to owning a second company that performed source emission testing – all over a mere forty years.
Along the way, Mr. DeFriez continued to be involved in corrosion projects, eventually applying to be grandfathered into the new California Profession Engineer’s Corrosion Engineering specialty. Over the years, he has been the principal engineer in a number of legal involvements, only a few resulting in testimony in court (best way to do it). As he likes to say, “I have always won my cases, sometimes by a positive judgment and sometimes by telling my client that he has no chance, so don’t spend any more money”.
In the environmental field, Mr. DeFriez has gathered three patents, one for an analytical procedure and two for instruments or sampling equipment. His association with I-ENG-A is through this company. Since he really enjoyed the investigative aspect of corrosion projects, he considered the prospect of investigative engineering past his retirement age a positive development to keep him active and alive (needed since he has a much younger Chem E wife who wants him around for some while).